Most tin bronze parts are produced from premixes although some are made from pre-alloyed powder. Since prealloyed powders have higher yield strengths and work hardening rates than premixed powders, the pressing loads required to achieve a given green density are higher than those required when pressing elemental powders. The differences in pressing characteristics of premixed and prealloyed powders are indicated in Figure 6.
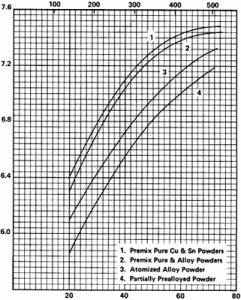
characteristics-properties-copper powder
Processing variables influence the properties. In an investigation in which 90Cu-10Sn and 88.6Cu-9.9Sn-1.5C (graphite) premixed powders were used, the optimum strength was achieved when the tin-rich phase was completely alloyed with the copper but little grain growth had occurred. Figure 7 shows the effect of density and graphite content on the strength of the bronze.
Properties of tin bronze P/M parts are influenced also by such factors as heating rate and sintering time and temperature. Faster heating rates tend to produce greater growth than slow heating rates. Sintering temperature influences both growth and strength. Sintering time influences dimensional control and strength; rapid growth occurs at the beginning of sintering and is followed by a period of predictable slow shrinkage. By completing sintering in the shrinkage range, it is possible to maintain dimensional control over the bronze P/M product.
Bearings
A unique attribute of powder metallurgy is the ability to produce porous products with interconnected porosity. This attribute made possible the development of the self-lubricating bronze bearing, an early P/M product, the first having been used in a Buick automobile in the 1920s. Depending on the sintered density, these bearings can absorb from 10% to 30% by volume of oil and can supply a continuous lubricating film even at low speeds. Porous bronze bearings also have the advantage that they are sufficiently ductile to permit assembly by ring staking.
Development of these bearings revolutionized the home appliance industry. By eliminating the requirement of periodic lubrication, the self-lubricating bearing assured many years of trouble-free operation of home appliances and led to a great expansion of the industry. New applications continue to be found and the self-lubricating bronze bearing industry consumes a major portion of the copper powder produced each year.
Self-lubricating porous bronze bearings depend on conduction and convection for heat dissipation during service. The frictional heat developed is proportional to PVµ where P is the pressure on the bearing, V is the surface velocity and µ is the coefficient of friction. Practical limits for safe operation of these bearings are often set at a PV factor of 50-60 ksi (345-414 MPa). These bearings are installed by pressing into rigid reamed or bored housings.
Porous bronze bearings are used widely in automotive service, household appliances, automatic machines and industrial equipment in two types of applications:
For low-duty shaft bearings where the static load-carrying capacity is adequate; where lubrication is impossible; and where the only requirement is low cost and avoidance of heating, seizure or squeaking throughout the life of the appliance or machine.
As an alternative to an oil bottle or ball bearing in medium to heavy duty applications. In these applications, facilities for relubrication must be supplied. 3
There are many other uses for these bearings. For example, in space vehicles, bronze P/M bearings have been used as sleeve bearings for attitude control mechanisms, solar panel hinges and stepping device bushings in tape recorders and commutators.
Filters
The ability to achieve close control of porosity and pore size is the basis for the use of metal powders as filters. Most producers prefer spherical powder of closely controlled particle size to permit the production of filters within the desired pore size range. Tin bronze is probably the most widely used filter material but nickel silver and copper-nickel-tin alloys are also used. The effective pore size can be varied widely but for P/M filters generally ranges from 5-125 microns. P/M bronze filters can be obtained with tensile strengths ranging from 3-20 ksi (21-138 MPa) and appreciable ductility, up to 20% elongation. In addition, P/M bronze has the same corrosion resistance as cast bronze of the same composition and, therefore, can be used in a wide range of environments.
P/M bronze filters are used to filter gases, oils, refrigerants and chemical solutions. They have been used in fluid systems of space vehicles to remove particles as small as one micron. Bronze diaphragms can be used to separate air from liquids or mixtures of liquids that are not emulsified. Only liquids capable of wetting the pore surface can pass through the porous metal part.
Bronze filter materials can be used as flame arrestors on electrical equipment operating in flammable atmospheres where the high thermal conductivity of the bronze prevents ignition. They can also be used on vent pipes on tanks containing flammable liquids. Here again, heat is conducted away so rapidly that the ignition temperature is not reached.
Aluminum bronze P/M parts containing from 5% to 11% aluminum are prepared from blends of the elemental powders. Alloys containing from 5% to 9% aluminum are single-phase materials and have excellent ductility. They can be strengthened by cold working. Alloys containing from 9% to 11% are two-phase materials which are less ductile than the alloys of lower aluminum content. However, they can be heat treated to increase their strengths.
The sintered yield strength increases from 11 ksi (26 MPa) at 7% aluminum to 40 ksi (276 MPa) at 11% aluminum; heat treatment of the latter alloy increases the yield strength to 60 ksi (414 MPa). Tensile strengths increase uniformly from 32 ksi (221 MPa) for the 7% alloy to 65 ksi (448 MPa) for the heat treated 11% alloy. Elongations of the 5% to 9% alloys are in the 25-35% range; the two phase alloys are considerably less ductile. 4 These properties make the P/M aluminum bronzes suitable for the production of parts where the strength requirements are too high to be met by the tin bronzes.
Limited corrosion data indicate that these P/M aluminum bronzes have properties similar to those of the cast and wrought counterparts. With this combination of strength and corrosion resistance, the alloys can be used for the production of P/M parts such as impellers, gears, connecting rods and similar components.